The Future of Prefabricated Buildings in Bangladesh
Md. Joynal Abdin*
Business Consultant & Digital Marketer
Founder & CEO of Trade & Investment Bangladesh
The construction industry is on the cusp of a revolution, and at the forefront of this transformation is the concept of prefabricated buildings. Prefabrication, often referred to as prefab or modular construction, involves assembling components of a structure in a controlled environment before transporting them to the construction site. As Bangladesh grapples with the challenges of rapid urbanization, environmental concerns, and the need for cost-effective and efficient construction methods, the exploration of the future of prefabricated buildings becomes increasingly pertinent.
Definition and Concept of Prefabricated Buildings:
Prefabricated buildings are constructed using pre-manufactured components that are produced off-site and then transported to the construction location for assembly. These components can range from structural elements like walls, floors, and roofs to entire room modules. The key distinction lies in the controlled environment of the manufacturing facility, where factors such as temperature, humidity, and quality control are closely monitored. This precision in fabrication ensures that each component fits seamlessly with others during on-site assembly, resulting in a more efficient and streamlined construction process.
The concept of prefabrication isn’t new to the global construction industry. Dating back to ancient civilizations, elements of buildings were often pre-fabricated and assembled on-site. However, the modern era has witnessed a significant evolution in prefabrication techniques, driven by technological advancements and the need for faster, more cost-effective construction methods.
Brief History of Prefabrication in Bangladesh:
In the context of Bangladesh, the history of prefabrication is a journey marked by progressive innovation. The utilization of prefabricated elements gained traction in the latter half of the 20th century. Initially, simple components like concrete panels were manufactured off-site and transported for on-site assembly. Over time, the construction industry in Bangladesh has witnessed a gradual shift towards more sophisticated prefabrication techniques, incorporating steel, modular construction, and advanced materials.
The early 21st century saw a surge in prefabrication projects, especially in response to the increasing demand for housing and infrastructure. Bangladesh, like many other developing nations, faced challenges related to rapid population growth and urbanization. Prefabrication offered a solution to accelerate construction timelines, reduce costs, and minimize environmental impact.
Significance and Relevance of Exploring the Future of Prefabricated Construction:
- Rapid Urbanization: Bangladesh is experiencing unprecedented urbanization, with a significant percentage of the population migrating to cities. Prefabricated construction provides a rapid and scalable solution to address the housing needs of this burgeoning urban population. By reducing construction timelines, prefab methods can contribute to timely and efficient housing development.
- Cost-Effectiveness: Traditional construction methods often entail higher costs due to extended timelines and increased labor requirements. Prefabrication streamlines the construction process, resulting in cost savings through reduced labor, less waste, and optimized resource utilization. In a country where economic considerations are paramount, the cost-effectiveness of prefab construction is of immense importance.
- Environmental Sustainability: With a growing awareness of environmental issues, the construction industry is under pressure to adopt more sustainable practices. Prefabrication inherently reduces on-site waste, as components are precisely manufactured to fit the required specifications. Additionally, the controlled manufacturing environment allows for the implementation of eco-friendly materials and processes.
- Quality Control: The controlled conditions of a factory setting ensure a higher level of quality control in prefabrication. This is particularly significant in regions prone to extreme weather conditions or seismic activities, where structural integrity is paramount. Prefabrication minimizes the risk of defects and ensures that each component meets stringent quality standards.
- Timely Infrastructure Development: As Bangladesh strives for comprehensive infrastructure development, prefabricated construction offers a faster and more efficient means of realizing ambitious projects. From bridges and commercial buildings to educational institutions, the timely completion of infrastructure projects is crucial for the country’s progress.
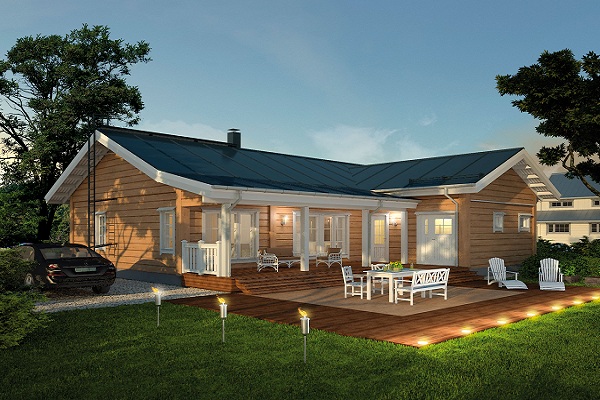
Current State of Construction in Bangladesh:
Traditional construction methods have been employed for centuries, forming the backbone of the built environment across the globe. While these methods have demonstrated durability and functionality, they also come with inherent limitations that impact both the environment and the economy.
One of the primary limitations of traditional construction methods lies in their resource-intensive nature. Traditional buildings often rely on materials such as concrete and steel, which require significant amounts of energy to manufacture. The extraction, transportation, and processing of these materials contribute to high carbon emissions and environmental degradation. Additionally, the depletion of natural resources, such as timber for traditional wooden structures, raises concerns about sustainability.
Furthermore, traditional construction practices often lack efficiency in terms of time and labor. The manual labor involved in these methods can lead to prolonged construction periods, causing delays and increased costs. Skilled labor shortages also pose challenges, as the demand for experienced craftsmen may exceed the available workforce, resulting in compromised construction quality.
Environmental challenges associated with traditional construction methods extend beyond material use. The energy consumption during the construction phase and the subsequent operational phase of buildings contribute significantly to carbon emissions. Inefficient insulation and ventilation systems in traditional structures can further exacerbate energy consumption, leading to higher utility bills and increased strain on the environment.
Economically, traditional construction practices face challenges related to cost and affordability. The high upfront costs of materials and labor can be prohibitive for many individuals and communities, limiting access to safe and sustainable housing. Additionally, the long-term maintenance costs of traditional buildings may surpass those of more modern and energy-efficient structures, impacting the economic viability of these constructions over time.
The environmental and economic challenges of traditional construction methods have prompted a shift towards more sustainable and innovative alternatives. Green building practices, including the use of eco-friendly materials and energy-efficient designs, aim to mitigate the environmental impact of construction. Prefabrication and modular construction methods offer advantages in terms of speed and efficiency, reducing both construction time and costs.
Adopting environmentally friendly construction materials, such as recycled steel, bamboo, or engineered wood, can contribute to sustainable building practices. Moreover, incorporating renewable energy sources, such as solar panels, and implementing energy-efficient technologies can significantly reduce the carbon footprint of buildings.
Global Trends and Influences:
Prefabricated construction, often referred to as modular or off-site construction, has gained significant traction internationally as a sustainable and efficient alternative to traditional building methods. This approach involves manufacturing components off-site and assembling them on-site, offering numerous advantages in terms of time, cost, and environmental impact.
Overview of International Trends:
Across the globe, there is a growing emphasis on prefabricated construction as a means to address various challenges associated with traditional building practices. One prominent trend is the use of advanced technology and digital tools in the design and fabrication processes. Computer-aided design (CAD) and Building Information Modeling (BIM) enable precise planning and customization, resulting in high-quality modular components.
Additionally, sustainability has become a central focus in prefabricated construction. Many countries are exploring eco-friendly materials, such as recycled steel and engineered wood, to minimize environmental impact. The reduced waste generated during the manufacturing process and the potential for energy-efficient designs contribute to a more sustainable construction industry.
Case Studies from Countries with Successful Prefabrication Initiatives:
- Sweden: Sweden has been a pioneer in embracing prefabricated construction techniques. BoKlok, a joint venture between IKEA and Skanska, has successfully implemented a large-scale modular housing initiative. The company utilizes standardized components and streamlined processes to construct affordable, energy-efficient homes. This approach has not only reduced construction costs but also significantly accelerated the pace of housing development.
- Singapore: Singapore has faced challenges associated with limited land availability, prompting the government to explore innovative construction solutions. The use of Prefabricated Prefinished Volumetric Construction (PPVC) has gained prominence. This method involves manufacturing entire rooms or apartment units off-site, including finishes and fixtures. The pre-finished components are then transported to the construction site for assembly. Singapore’s commitment to prefabrication has resulted in faster project delivery, less disruption to the surrounding environment, and improved construction quality.
- China: China, with its rapid urbanization and large-scale infrastructure projects, has embraced prefabricated construction as a strategic approach. The government has encouraged the use of modular construction for residential and commercial buildings. Notable examples include the construction of a 57-story skyscraper in just 19 days using prefabricated components. China’s focus on mass production and standardization has led to increased efficiency and cost savings in the construction sector.
- United States: In the United States, the demand for affordable and sustainable housing solutions has fueled interest in prefabricated construction. Companies like Katerra and Plant Prefab are leveraging advanced manufacturing techniques to produce high-quality, customizable modular homes. This trend is not limited to residential construction, as the use of prefabrication is expanding in commercial and institutional projects as well.
These case studies highlight the diverse applications and success stories of prefabricated construction on an international scale. The trend towards off-site manufacturing and assembly is driven by the desire for faster construction, cost savings, and a reduced environmental footprint. As technology continues to advance and global construction needs evolve, prefabricated construction is likely to play an increasingly crucial role in shaping the future of the built environment.
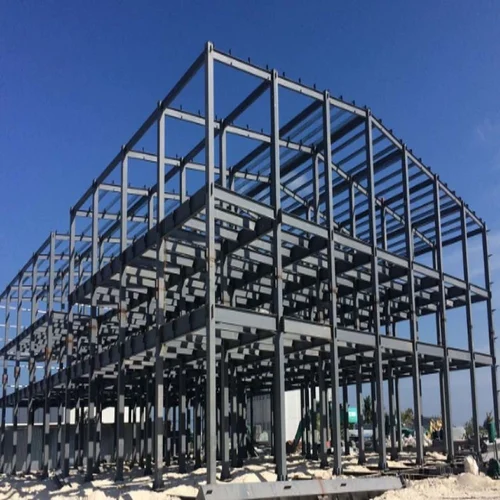
Technological Advancements:
The role of technology in advancing prefabricated construction is transformative, reshaping the way buildings are designed, fabricated, and assembled. Integrating smart technologies and sustainable practices into prefabricated construction not only enhances efficiency but also contributes to the creation of more intelligent, eco-friendly structures.
- Design and Planning: Technology plays a pivotal role in the initial stages of prefabricated construction by improving the design and planning processes. Computer-aided design (CAD) and Building Information Modeling (BIM) enable architects and engineers to create detailed digital representations of structures. This not only ensures precision in component manufacturing but also facilitates efficient collaboration among project stakeholders.
- Robotics and Automation: The use of robotics and automation in prefabricated construction enhances production speed and accuracy. Automated systems can precisely cut, shape, and assemble building components with minimal error, reducing waste and improving overall quality. This level of precision is especially crucial in the context of prefabrication, where components need to fit together seamlessly during on-site assembly.
- 3D Printing: 3D printing technology is making inroads in prefabricated construction, allowing for the creation of intricate and customized components. This additive manufacturing process can be employed to produce structural elements with complex geometries, offering architects and designers greater flexibility in realizing innovative and efficient designs. 3D printing also contributes to sustainability by minimizing material waste.
- Internet of Things (IoT): The integration of IoT devices in prefabricated construction brings a new level of connectivity and intelligence to buildings. Smart sensors and devices can be embedded in prefabricated components, enabling real-time monitoring of structural health, energy usage, and overall performance. This data can inform predictive maintenance strategies, enhancing the longevity and efficiency of the constructed structures.
- Sustainable Materials and Practices: Advancements in sustainable materials play a crucial role in aligning prefabricated construction with environmentally conscious practices. Technologies that facilitate the use of recycled or renewable materials, such as cross-laminated timber (CLT) and bamboo, contribute to reducing the environmental impact of construction. Sustainable practices, such as energy-efficient designs and the incorporation of renewable energy sources, further enhance the ecological footprint of prefabricated buildings.
- Prefabricated Prefinished Volumetric Construction (PPVC): PPVC, as mentioned in the case study of Singapore, exemplifies the integration of smart technologies into prefabricated construction. This method involves the off-site manufacturing of fully finished modules, including interiors and fixtures. The precision achieved through this approach results in higher-quality finishes, and the completed modules can be easily transported and assembled on-site, minimizing construction time and site disruption.
- Energy Management Systems: Smart technologies also extend to energy management systems within prefabricated buildings. Integration of energy-efficient HVAC systems, lighting controls, and smart thermostats optimizes energy consumption, contributing to sustainability goals and reducing operational costs over the building’s lifecycle.
Architectural Innovation:
Design possibilities and architectural flexibility in prefabricated buildings have evolved significantly, challenging the notion that modular construction is limited to standardized, simple structures. Innovations in materials, technology, and design approaches have expanded the creative potential of prefabricated buildings, allowing architects to push boundaries and create aesthetically pleasing, functional, and sustainable structures.
To read 2nd part of this article, click here!
The Future of Prefabricated Buildings in Bangladesh: The Future of Prefabricated Buildings in Bangladesh
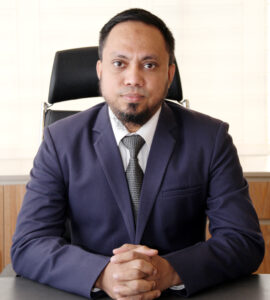
Mr. Md. Joynal Abdin stands as a prominent Business Consultant and Digital Marketer hailing from Dhaka, Bangladesh. He holds the role of Founder and CEO at Trade & Investment Bangladesh. With an extensive professional journey, he has contributed significantly, having served as Executive Secretary at Dhaka Chamber of Commerce & Industry (DCCI), Executive Director at DCCI Business Institute (DBI), Deputy Manager at SME Foundation, and Assistant Secretary at the Federation of Bangladesh Chambers of Commerce & Industry (FBCCI).
Mr. Abdin’s diverse array of services encompasses, but is not confined to, Business Research and Documentation, such as Feasibility Studies, Project Proposal Preparation, and Business Manual and Standard Operating Procedures writing. He is also adept at Export Market Selection, Product Positioning both domestically and internationally, Buyers-Sellers Matchmaking, Website Development, Search Engine Optimization (SEO), and Social Media Marketing, among other valuable offerings.